- By 小编
- 2025-07-28 08:46:44
- 技术支持
AGV:现代工厂智能物流的神经系统
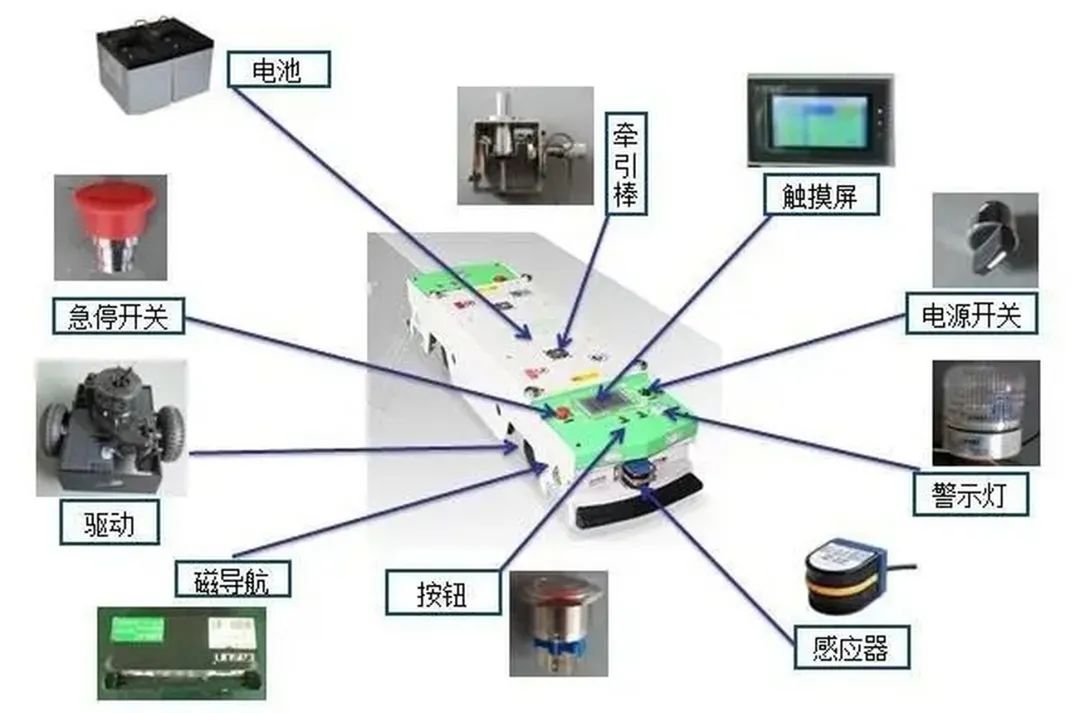
一、技术架构:感知-决策-执行的闭环进化
环境感知层的突破奠定了智能化基础。传统磁导技术依赖预埋磁轨,虽在固定路径场景(如仓库主干道)中稳定性达99.5%,但改造灵活性不足;激光SLAM导航通过三维点云实时建图,使AGV在特斯拉工厂的柔性产线中动态适应设备布局调整,路径重置效率提升40%;视觉导航系统凭借±5mm定位精度,支撑华为SMT产线实现印刷电路板的精准配送,良品率提升至99.99%。
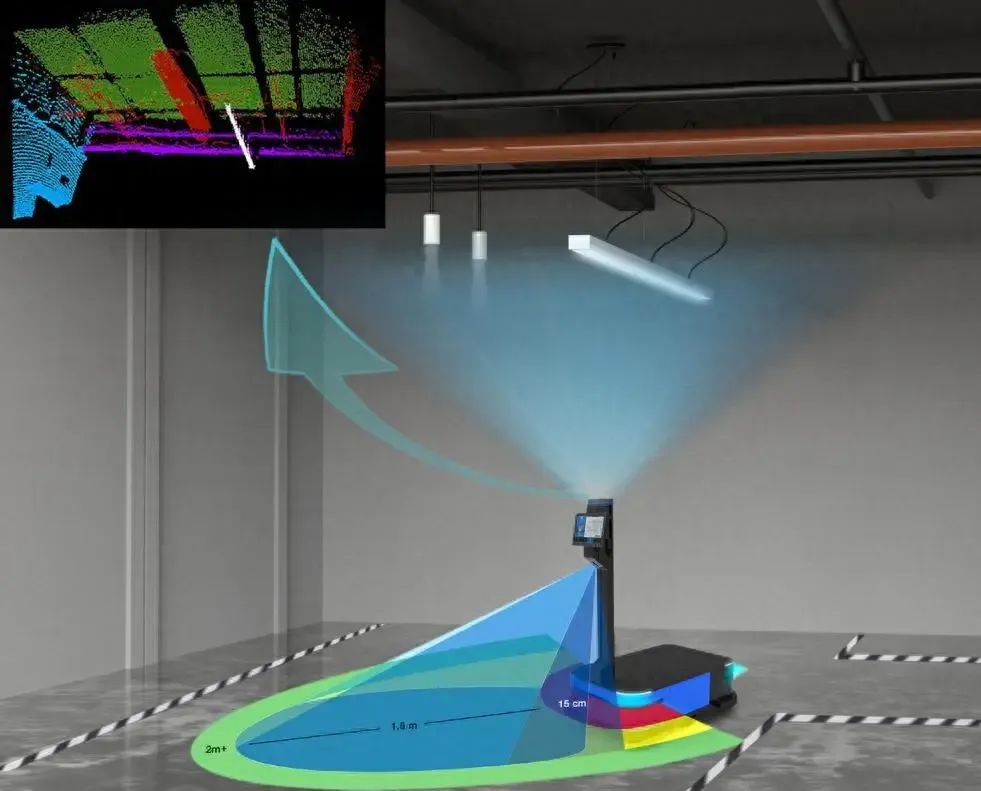
决策中枢的算法进化释放系统潜能。动态任务分配引擎融合订单数据与AGV实时状态(电量、负载、位置),采用改进蚁群算法将空驶率压缩35%;多车协同通过分布式时间窗调度,在长城汽车总装线上协调52台AGV同步配送发动机与座椅,冲突率降至0.1%;路径规划模块以DWA(动态窗口法)实现毫秒级重规划,狭窄通道通过率从75%跃升至92%。
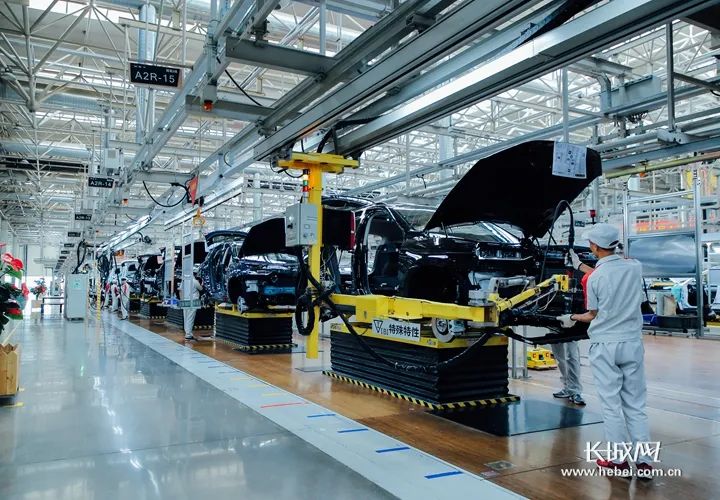
执行机构的机电融合保障可靠运行。高扭矩伺服电机配合防振底盘设计,使载重能力突破2吨,满足重型机械部件搬运需求;双冗余控制系统确保在化工车间等危险环境中连续运行10,000小时无故障。
二、场景落地:刚需驱动的价值裂变
在汽车制造领域,AGV与机械臂组成无缝协作单元。特斯拉上海工厂采用集群调度AGV完成电池包全自动转运,人工干预归零的同时装配节拍缩短28%。
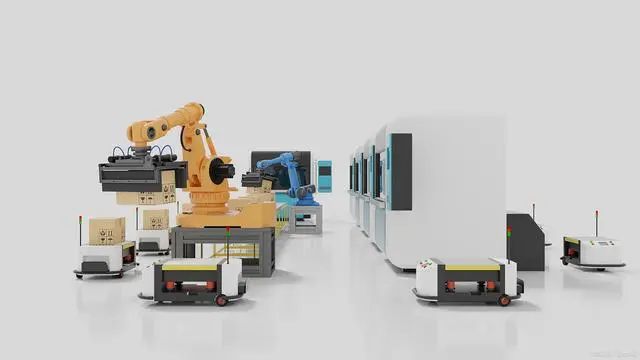
电子精密制造对毫米级精度提出极致要求。富士康深圳工厂部署视觉导引AGV,在千级洁净环境中将芯片模组配送定位误差控制在±0.8mm,物料周转效率提升50%。
仓储物流革命因“货到人”模式加速。京东亚洲一号仓运营的300台激光SLAM AGV集群,实现24小时不间断货架搬运,拣选效率较传统模式提升300%,差错率降至0.005%。
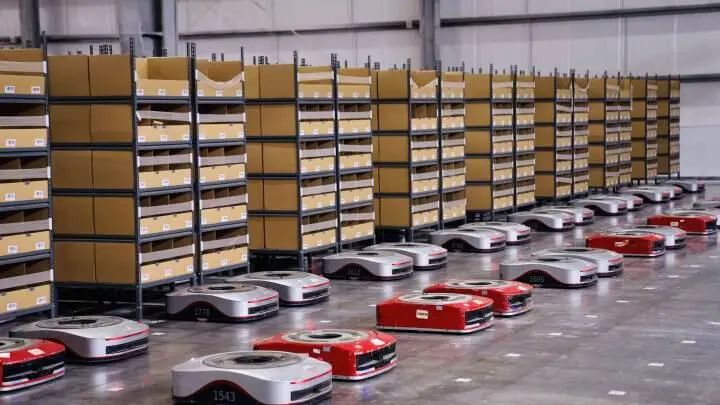
高危场景更凸显不可替代性。中石化齐鲁基地采用防爆型AGV运输苯类化学品,彻底消除人工接触风险;中芯国际无尘车间内,特殊密封设计的AGV满足Class 100洁净标准,晶圆污染事件归零。
三、前沿突破:自主进化的三大方向
算法融合创新正突破复杂环境限制。A*(A-Star)全局路径规划与DWA局部避障的混合算法,使上汽大众工厂AGV在设备故障时自主切换备用路线,响应速度提升50%;多目标优化模型通过TOPSIS加权算法平衡能耗与时效,菜鸟嘉兴仓拥堵率下降80%。
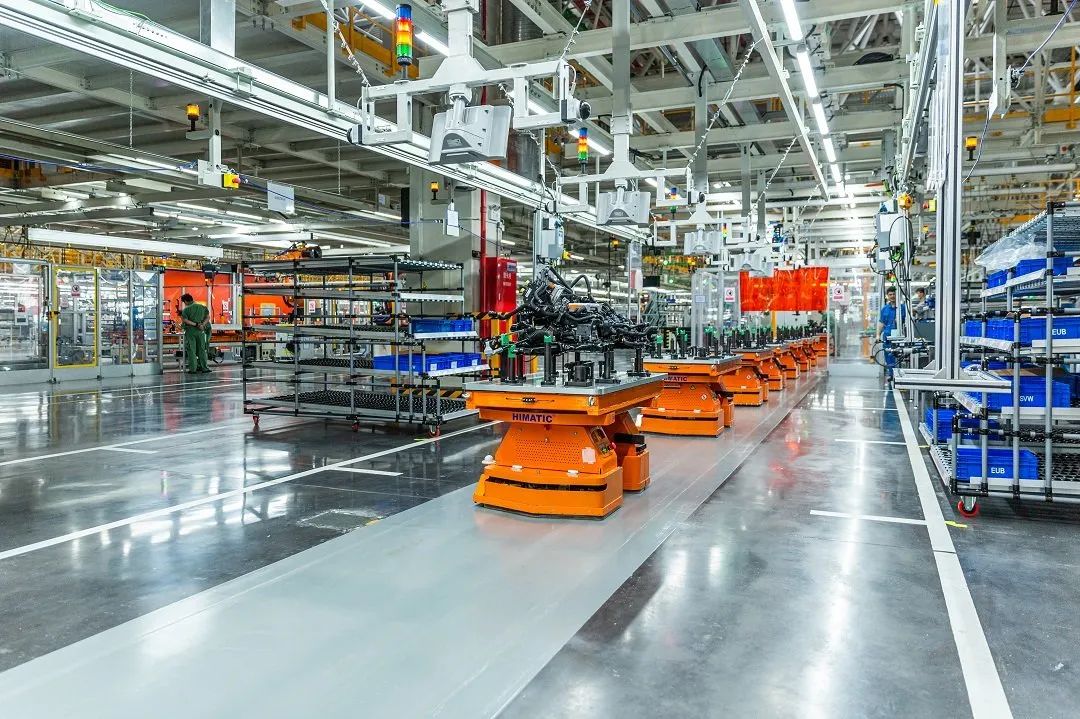
系统深度集成重构生产逻辑。基于OPC UA协议,一汽大众MES系统直接向AGV群下发配送指令,订单响应缩至5分钟;顺丰中转场应用数字孪生技术预演AGV运行,调试周期从两周压缩至72小时。
自主决策能力开启认知革命。阿里巴巴菜鸟仓库部署的深度Q网络(DQN)算法,使AGV通过强化学习自主优化货架搬运策略,试运行三月后效率再提15%;博世苏州工厂结合5G边缘计算,将决策时延压至20毫秒,彻底摆脱云端依赖。
本质重构:从工具到生产力基座
AGV的技术跃迁正推动工厂物流实现三重质变:
效率升维:最大提升300%作业效能,拣选成本下降40%
精度革命:定位精度突破亚毫米级,产品良率逼近100%
安全颠覆:高危场景100%替代人工,事故率归零
随着自适应学习与跨系统融合深化,AGV将从“物流执行载体”进化为“生产决策节点”,最终成为智能工厂的自主化神经中枢。
技术预言:当AGV集群通过联邦学习共享经验时,全球首个无人决策工厂将在2028年前诞生——这不仅是物流变革,更是制造范式的重构。